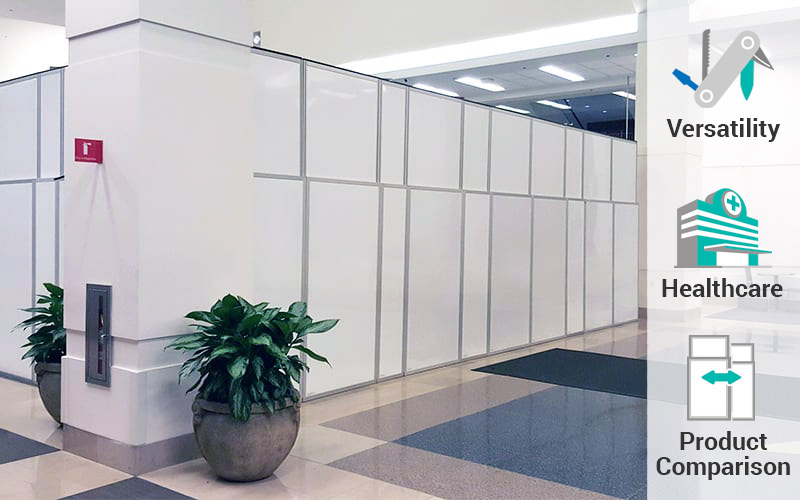
It’s easy to miss the many important changes with modular temporary containment for occupied healthcare renovations. And, the measuring sticks for grading temporary containment have advanced – significantly – and quickly. We talk about this a lot around here – and with our customers.
We asked our VP of Business Development (and STARC employee #3), Chris MacKenzie to help guide us through key changes and what continues as constant markers for modular temporary containment. Chris has been on the ground, learning from our healthcare contractor and facilities customers for over six years and is basically a walking Wikipedia for modular temporary containment.
What are the constant and new markers of containment for healthcare occupied renovation and how has modular temporary containment evolved within just the last 5 years?
First: what are the constants?
- Balancing time and cost. With project margins in the low single digits, this has always been a factor. Temporary containment (like drywall) that is time-consuming and labor intensive to install and demolish is a double-edge sword in healthcare settings: it negatively impacts project margins and amplifies disruption to patients and staff. That’s precisely why we engineered our solutions to go and up come down faster and easier than alternatives and without noise, dust or scheduling disruptions.
- Safety of patients and staff during a renovation has always been at the forefront for occupied renovations in sensitive healthcare environments. Infection Control Risk Assessment (ICRA) requirements have become increasingly prioritized since the first genesis was publish by AIA Guidelines for Design and Construction of Health Care Facilities in 2001. Other safety standards, such as fire codes and ratings, are also always a top priority. What’s evolved is how we can achieve these requirements – which we’ll talk about next.
- Flexibility of installation and the need to create containment around a myriad of infrastructure designs is always a significant factor for healthcare facility renovations.
Next: What’s New?
- Heightened Safety Measures & Awareness. A significant advancement is ‘safety first’ and patient satisfaction being designed into containment solutions. The pandemic has obviously magnified the importance of safety first approach. In the renovation world, we’ve seen the role and influence of Facilities Managers and Infection Preventionists increase – a trend which will likely carry forward. For contractors, this means the importance of having a temporary containment solution that meets safety requirements is now more than assumed, it’s often an essential make or break. In fact, solutions used 5 years ago are no longer even in the consideration set.
-
- Plastic sheeting, for example, is essentially considered a non-starter for healthcare containment at this point. While it goes up quickly, it fails across the board for essential ICRA safety requirements due to lack of an airtight seal and being easily torn – both leading to airborne particles easily escaping the construction zone. An IP’s nightmare.
Infection Preventionist, Dr. Janet Haas recalls one of these instances: “We used reinforced plastic to separate a construction area from our oncology unit, and came in to find that someone on the night shift had sliced through the plastic to get into or out of the construction designated area.”
- Zippered walls also present a significant risk of failing to contain a zone properly. “There are many very common (zipper) occurrences, such as the zip wall zippers being left open (all the time) and the plastic either not secured to every wall/ceiling when poles are used to secure it, or the tape falling off over time.” – Dr. Janet Haas
- And drywall, often the default standard, actually creates more safety risks than it solves by creating dangerous dust during setup and take-down. In fact, the National Institute of Health’s training program in Environmental Health Sciences estimated over 2 million incidences of Healthcare Associated Infections and 99,000+ deaths annually from opportunistic pathogens – a portion of which are directly related to hospital maintenance and renovation. One of those pathogens, Aspergillus, is ‘found naturally [in many things] including drywall, plaster, dust, and concrete powder.
- Plastic sheeting, for example, is essentially considered a non-starter for healthcare containment at this point. While it goes up quickly, it fails across the board for essential ICRA safety requirements due to lack of an airtight seal and being easily torn – both leading to airborne particles easily escaping the construction zone. An IP’s nightmare.
To address these safety challenges and heightened needs, we designed infection prevention and fire safety requirements into our temporary containment system. Our solutions exceed ICRA Class IV (the most stringent) and meet both ASTM-E119 and ASTM-E84 requirements.
- Modular Design Advancements: Design capabilities in modular temporary containment have evolved and advanced significantly in the last 3-5 years. Early iterations of temporary containment used more problematic components to deliver modular designs – which have critical hospital environment implications. For example, we hear stories from the field about problems with knobs getting lost and sticking out, or worse: causing gaps between panels and faulty seals – posing dangerous pathogen release risks.
We saw this as an opportunity for advancement. Our tongue and groove assembly allows for a simple lift and drop, single tool and knob-less installation. This results in faster, easier setup and take-down and most importantly: an ICRA-compliant, airtight seal. Our modular design also features telescoping height capabilities and superior reconfigurability.
- Durability: Drywall and polycarbonate have traditionally been considered as a durable containment choice. In reality, breaches or punctures from common hospital events occur frequently with both – and facilities are increasingly aware of this problem.
“While stronger than plastic sheeting, we have seen standard hospital equipment like gurneys inadvertently break through a polycarbonate wall – creating safety hazards and breaking any airtight seals that may have initially formed,” Chris recalled.
Drywall breaches pose significant containment threats, as our customer Peter Hauer, Field Superintendent at Mortenson, explains: “With a conventional temporary wall installation like drywall, if you bumped into it you would have cuts and tears. There’s no infection control when there’s a breach in the wall that can lead to the potential of dust and contaminants.”
We solved for this. We use the most durable materials to engineer our temporary containment solutions, resulting in unparalleled sturdiness and longevity. Our ‘hospital bed proof’ modular temporary containment system can take 200 lbs of force without moving an inch. Everything we produce is warrantied for up to three years and for hundreds of uses.
- Green: the importance of making environmentally conscious product and business decisions is skyrocketing. One-time use options like drywall just end up in the landfill and known as the single biggest source of waste in construction. Our solutions are designed with the environment in mind: they can be reused for hundreds of projects and many years – and produced with 100% renewable energy and a 0 carbon footprint.
- Importance of aesthetics: more and more we’re hearing from customers that the way containing a renovation looks is a priority for patient and staff wellbeing. When lesser solutions are in place like unfinished drywall or plastic, clients ‘notice’ the renovation more. Beyond being a big distraction, if a project looks less buttoned up key leadership may ask the dreaded ‘is something is going wrong with this’ question – and patients may feel less safe. Our temporary containment is designed to blend in and look like part of the building. We also often hear how much hospital staff love the modern, clean look of our modular walls.
- Reusability: contractors and facilities managers are increasingly realizing the value of reusable temporary containment solutions. We’re seeing a distinct shift away from choosing one-time-use options and toward solutions like ours, which can be redeployed across an endless number of configurations like facility maintenance projects, renovations, isolation/emergency preparedness, capacity surges and space repurposing. In addition to multiple applications, our solutions are designed to be reused for years and years of projects. Our customers typically recover their investment after completing 3-5 projects – and the investment quickly becomes a revenue stream. Read how our customer W.E. Bowman Construction, is reusing our products and proving ROI.
What makes the grade today when compared against both long-standing and new markers?
We know – another matrix. This time, it’s completed for you with helpful grades for long standing and new temporary containment markers.
|
STARC | Drywall | Poly | Plastic Sheeting |
Initial Cost | B- | B | B | A |
Ongoing Cost / ROI | A | E | D | E |
Fast Install | A | C | B | A |
Safety Requirements | A | C | C | E |
Safety First | A | D | C | E |
Modular, fit any prebuilt environment | B+ | A- | C | C |
Durability, Reusability | A | E | C | D |
Green | A | D | C | D |
We want to leave you with this: you no longer have to settle for problematic temporary containment solutions. In fact, many traditional solutions are no longer even viable options for healthcare environments. A higher standard exists and we are proud to offer it to you.