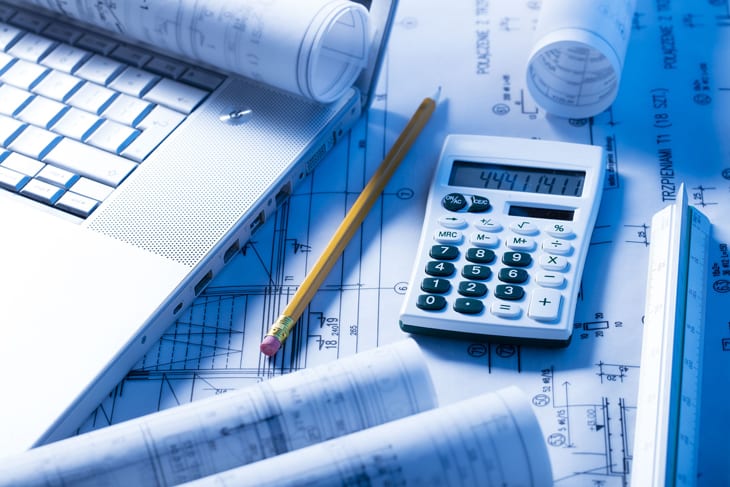
Written by Gearhart and Associates, LLC. for STARC Systems, Inc. Gearhart and Associates are industry experts in Infection Control Risk Assessment (ICRA) training, Infection Control and Prevention Strategies, and Facilities Risk Management.
“Health care facilities continuously face technology upgrades, efficiency improvements, and facility upgrades to meet patient needs and increase patient satisfaction. We see a rise across the board in construction and renovation projects to meet patient needs,” says Lourdes Sisk, Marketing Manager for The Gordian Group, Inc. (Health Facility Management)
In 2016, healthcare construction or renovation spending was on track to be between $6 billion and $7 billion according to Scott Creekmore, director of core accounts for The Gordian Group, Inc. Another Creekmore report showed data estimating that renovation spending will increase between $8 billion and $9 billion by 2020.
Multi-Phase Renovations Challenge Healthcare Organizations
In healthcare facilities (some over 900,000 square feet), renovations are generally done in phases to ensure that daily operations continue during construction. Contractors commonly use temporary walls to isolate compromised areas in a healthcare environment to perform remediation and renovation. However, traditional containment solutions such as plastic sheeting and drywall barriers have proved to be time-consuming, expensive, disruptive, and often ineffective.
Brian Campbell, regional manager of maintenance and construction for Central Maine Medical Center (CMMC) had this to say on a recent renovation in and around the facility’s emergency department that required a 100-foot airtight containment barrier around the construction zone.
“The traditional method of constructing this large of a containment barrier takes two to two-and-a-half days.”
Containment such as plastic sheeting and drywall barriers result in increased labor costs, due to the time it takes to install, dismantle, and reinstall for each phase, with some projects requiring up to 8-10 phases in total.
To install of 20 feet of drywall partition is estimated at 25 man-hours. Some poly barriers are estimated at 11 man hours. This amount of time limits the flexibility the crew needs to proceed with construction efficiency, while also driving up project labor and material costs.
STARC System Reduces Downtime and Labor Costs for Healthcare Construction
The STARC Temporary Containment System consists of reusable panels that are quickly installed, dismantled, and reinstalled to provide maximum flexibility. The system is designed to reduce downtime by reducing the containment installation phase from days to minutes.
After using the STARC System, Brian Campbell of CMMC said, “The 100’ of temporary wall (STARC) was constructed in less than an hour.”
The STARC reusable containment system demonstrates an ROI after 3 to 5 uses compared to drywall barriers and plastic construction. The system is reusable, with no waste disposal, and the panel components require no daily maintenance. STARC is a simple reusable engineered system that roughly takes two people one hour to install 100’ of wall.
Jeff Skrilow, CR, WLS with Damage Control Inc., a full-service disaster restoration company with 20 years experience in the healthcare space, praised the containment wall system on a recent Long-Term Care facility renovation project.
“It is very easy to install, dismantle, and reinstall without any dust or debris. STARC is the tool in our toolbox that is a differentiator for DCI. It’s been a game changer.”
Prior to using STARC, DCI was using sheetrock and metal studs, which Jeff mentions made for a satisfactory containment system, but the labor involved was hard work and time consuming, plus the installation created an issue with dust, which required a second containment system to be constructed, creating more labor costs.
The DCI team was able to install 50’ of containment wall in 30 minutes with no disruption which prevented the staff and occupants from having to relocate.
The system has proven to reduce labor and downtime between phases, which correlates to direct savings in project costs.
It eliminates the stress and concern of increasing costs, allowing for crews to assemble the barrier, get to work, and move on to the next phase seamlessly. It is a complete containment solution without supplemental materials and assembles with just one tool.
With healthcare renovation spending projected to rise, contractors and restoration companies can accept jobs with confidence, knowing they have game-changing technology in their arsenal that reduces labor and material costs and increases overall efficiency on the job.