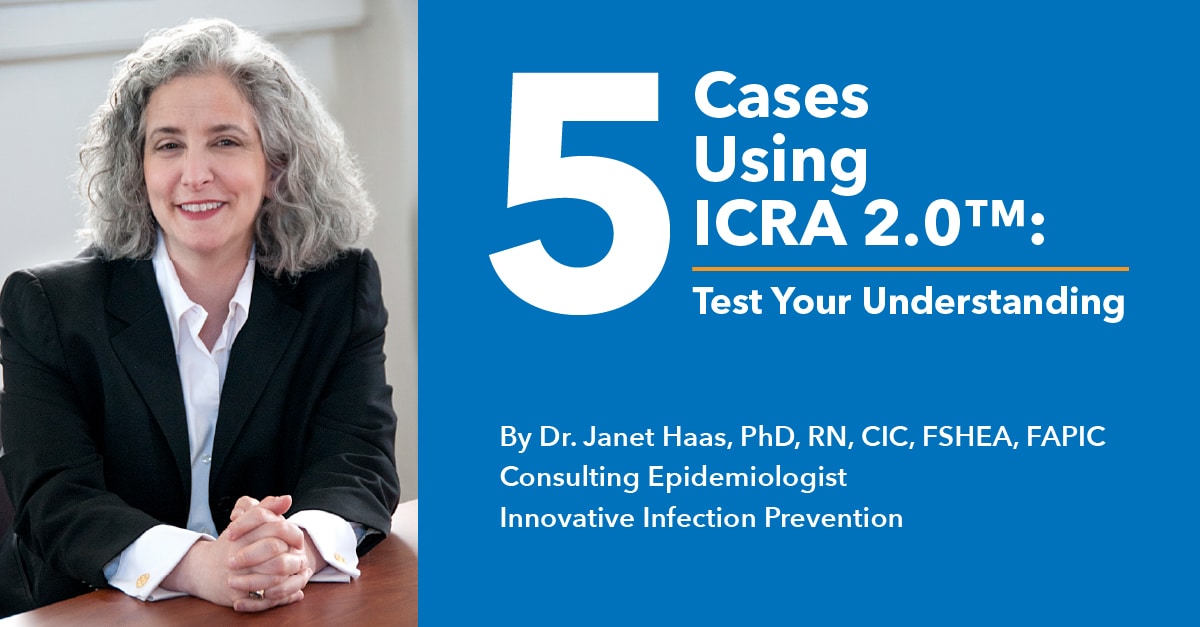
By JANET HAAS, PhD, RN, CIC, Principal Consulting Epidemiologist, Innovative Infection Prevention
The latest version of the infection control risk assessment has been called ICRA 2.0 to distinguish it from the original version that facility managers and infection preventionists have been using for several years. As mentioned in my previous blog post on this topic, ICRA 2.0 builds on many years of experience using the original ICRA and clarifies many areas that were not specifically addressed. In this post, we’ll apply ICRA 2.0 to some scenarios of construction and maintenance activities that are typical for healthcare facilities.
Using the tables below, try to decide where you think each scenario fits in the ICRA matrix, recognizing that there may be more than one answer depending on where the work will take place.
Open ICRA Reference TablesScenario 1: Fire Suppression System Inspection and Maintenance
The safety officer is working with the facility maintenance team to inspect and perform annual maintenance on the fire suppression system in the facility. They will need to open ceiling tiles to inspect the system and, if needed, perform any minor repairs. They anticipate opening 2-3 tiles in each patient care unit. Areas requiring more extensive repair or maintenance will be flagged for future work, which will be done by an outside contractor.
Question:
Which work type and construction class apply to this scenario?
Answer:
This work is Type A inspection with potential for very limited repairs, so in most areas it will be CLASS I construction. However, when you get into the highest risk units such as transplant, ICUs, ORs and so on, the work becomes CLASS III and extra precautions to provide active means for controlling dust are needed.
Comment: Some facilities find it easier to have a single process for inspection and maintenance activities, either because they are concerned about high-risk patients in areas outside of the designated highest risk units, or because they want to standardize to one method for easier training and accountability. Facilities are free to do this but should default to the highest level of protection needed. In the case of inspection, facilities may opt to conduct all inspections from a mobile containment unit that is equipped with a HEPA unit.
Scenario 2: Upgrade to Medical Gas and HVAC Systems
The facility received an emergency preparedness grant to upgrade the medical gas and HVAC systems in preparation for a possible surge of infectious patients. A general medical unit will be retrofitted to upgrade the oxygen. Private rooms will have an additional headwall with oxygen, suction and electrical outlets so that the rooms can accommodate 2 patients if necessary. This is an 18-room unit, and the project will take 2 months to complete.
Question:
Which work type and construction class apply to this scenario?
Answer:
This work is considered Type D, large scale renovation involving 2 or more rooms. Because the unit is a patient care unit (high-risk), the work is considered CLASS V construction.
Scenario 3: Room Refreshes in a Post-Partum Unit
The facility maintenance department will be doing room refreshes in the post-partum unit, one room at a time as they become available. The nurse manager is working with the team to hold one room open each day. The project will involve paint and patch repairs, floor burnishing and other minor repairs to fixtures as needed, as well as the installation of a new infant security system which will require wiring from a central hub to each room.
Question:
Which work type and construction class apply to this scenario?
Answer:
This one is a little tricky. The work is considered Type C because of the installation of the new infant security system that involves installation of new cable and electrical work. The work is being done in a high-risk area; therefore, the work is CLASS IV.
Comment: Usual patch and paint repairs that will take less than a shift to complete would be Type B construction, which would result in the work being CLASS III for high-risk areas, and CLASS IV for the highest risk areas. This scenario had the added cabling and electrical work, which bumped it up. Be aware of add-ons that may be needed in selected rooms or areas when routine maintenance is being performed. For example, adding dialysis capabilities, medical gases or other new systems to selected rooms or areas may be rolled into routine maintenance activities. This may increase the amount of dust and disruption that can be anticipated and therefore the construction class. Facilities may choose to upgrade the class for the affected rooms or they can bump up the class for all the rooms if standardization helps assure appropriate adherence in the highest risk situations.
Scenario 4: Addressing Mold in a Patient Room
While fixing a leaky toilet flush handle in a patient room, the plumber noticed some mold on the sheetrock behind the toilet. The supervisor notified building maintenance and bed management of the situation, and the room was closed for new patient admissions. The plan is to assess the extent of water damage and remediate the mold using an outside contractor.
Question:
Which work type and construction class apply to this scenario?
Answer:
Environmental conditions that could adversely affect patients include mold or water (gray or black water). The mold in a patient room automatically bumps this work up to CLASS V.
Comment: The patient room could possibly be used as the anteroom for the mold remediation in the bathroom, as long as mold damage or water damage didn’t involve the patient room and air flow could be adjusted appropriately. This scenario illustrates a common unexpected finding that may be discovered during small repairs or routine maintenance. Facility managers and maintenance personnel should always be on the lookout for unsafe environmental conditions that must be fixed as soon as possible.
Scenario 5: Electrical Installation in a Waiting Room (Outside ED)
A generous donor funded the installation of a phone charging station for the waiting room outside of the emergency department. There is a closet that will be repurposed to hold the charging unit. The work requires removal of a door and a steel closet rod from the closet, installation of an outlet from a nearby conduit and painting the closet interior. The work is estimated to take less than 1 shift to complete.
Question:
Which work type and construction class apply to this scenario?
Answer:
This is another tricky one. Let’s start with the type of work. This is small scale, short duration Type B work that would create minimal dust. Removing a door and steel closet rod are not big dust generators. Installation of an outlet requires cutting a small piece of sheetrock but should not generate a large amount of dust. The area is a waiting room, so the location is medium risk. Using the ICRA matrix, we get CLASS II construction. HOWEVER, CLASS II is the maintenance class and must never be used for construction or renovation. If this is considered a renovation, it would be bumped up to CLASS III.
Comment: The methods to assure that no dust or mold spores are liberated into the environment are key to the success of the project, regardless of the class designation. The ASHE minimum required infection control precautions provide a baseline from which to work and add on as necessary.
How did you do? Did you find the newer version of the ICRA easy to use? Can you think of some situations that will require your facility to plan differently? These scenarios were intended to show some common situations that are similar to those you are likely to see in your facility. The ICRA 2.0 gives much more detail and includes guidance for more areas and situations. Each facility will need to assess their own patient populations and resources and decide how best to implement these enhanced safety precautions during construction, maintenance and renovation.
Dr. Haas is Principal Consulting Epidemiologist at Innovative Infection Prevention and an associate editor of the American Journal of Infection Control (AJIC). She previously served as Director of Epidemiology at 3 academic medical centers, and as 2018 APIC President. Prior to beginning her nursing and infection prevention professional journey, Janet also worked as a Journeyman Millwright Mechanic and was a member of the Carpenter’s Union.
