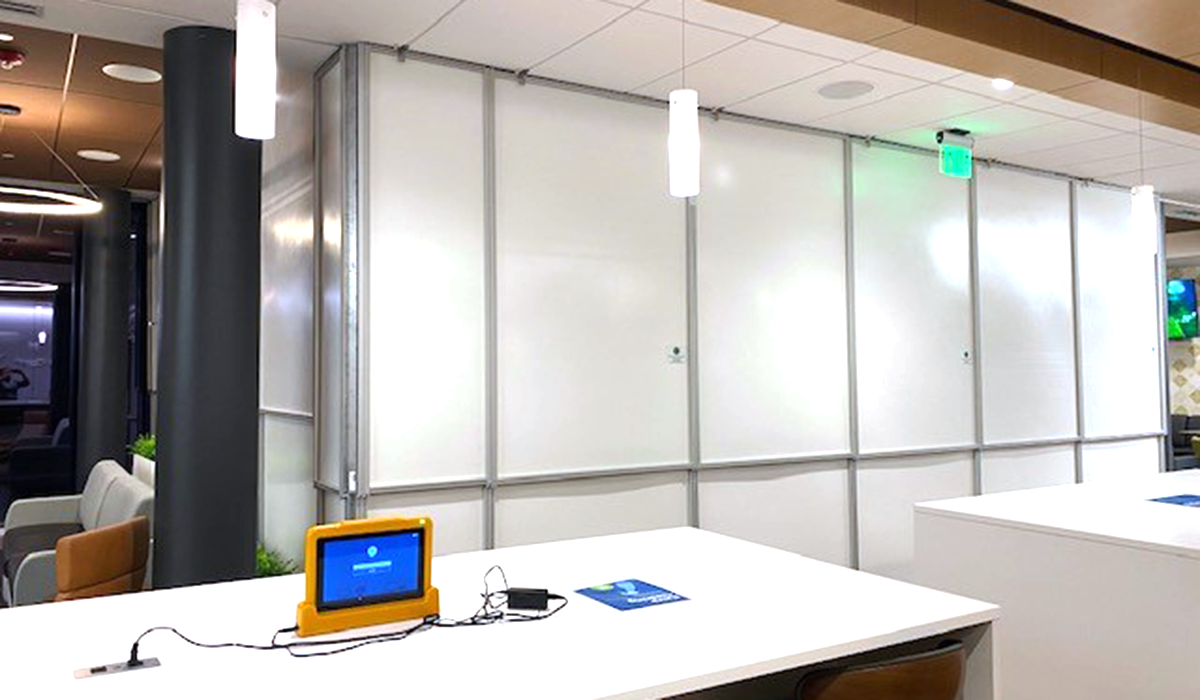
Renovations can be disruptive—noise, dust, delays—it’s enough to frustrate contractors, building occupants, and budgets alike. But what if there was a faster, cleaner, and more profitable way to contain dust and debris on jobsites? Enter high-quality temporary wall systems. Beyond containing dust and noise, these reusable temporary construction walls are improving jobsite efficiency and unlocking real profit potential for contractors.
High-quality temporary wall systems offer a number of key advantages on the jobsite:
- Fast-and-easy installation
- Flexibility for easy reconfiguration
- Reusable across dozens of projects
- Clean (and easily cleanable with common cleansers)
- No dust, debris, or disposal charges upon project completion
If your goal is to contain dust, debris, and noise on your jobsite, these temporary construction walls offer a no-brainer solution. But there’s another benefit to high-quality temporary walls: the durability of these systems unlocks profit potential.
A good example is RealWall™, our original, reusable temporary construction wall system. Valued for its sound attenuation, real wall appearance, and construction, RealWall reduces renovation noise up to 50% while exceeding ICRA Class IV/V and ASTM E-84 requirements. But, as the video below demonstrates, it’s also designed to last for years across hundreds of jobs.
Temporary Walls Enabling High Re-Use by Customers
Any manufacturer can claim its products are exceptionally durable. The question is, how well do the temporary walls in question hold up to the day-to-day demands of real-world construction sites?
To answer this question, STARC recently surveyed its customers to see just how many times they re-use our temporary wall systems from the initial point of purchase.

According to the survey results:
- 59% of long-time customers have re-installed 20 or more times since initial purchase.
- Another 15% of survey respondents said they reused their STARC temporary construction walls 10 or more times.
- Our customers purchased a temporary wall system once and redeployed it over and over again, typically recapturing their investment after just 3-5 uses.
Proof Is in the Field: Temporary Walls Improving ROI
Richmond, Va.-based W.E. Bowman is a recognized leader in healthcare construction. The firm’s healthcare clients require that all temporary construction walls exceed ICRA Class IV requirements.
Traditionally, W.E. Bowman used drywall and plastic walls to contain dust and debris, but while researching cost-effective alternatives that are environmentally sustainable, the firm discovered STARC. After trying one of our systems for a healthcare renovation, the firm’s ROI, relative to drywall, was as follows:
- Project required 5200’ of temporary walls spread over 7 phases
- The cost of STARC’s temporary construction walls was recaptured after 5 phases
- The overall savings for the project versus drywall was 75%
- W.E. Bowman plans to use the STARC panels they purchased on hundreds of more jobs
Building Best Practices—With Temporary Construction Walls
Beyond confirming that durability is one of the keys to unlocking profitability, the survey noted above reveals some clear-cut best practices.
For example, 67% of respondents charge for containment on a fee-per-linear-foot or per-phase basis. And upon project or phase completion, over 90% of respondents return the panels to a central storage area, with 44% quickly moving to re-install them on a new project within two to six weeks. Less than 10% report selling the panels or transferring them to the owner.
It’s easy to see how reusable temporary wall systems offer significant advantages over traditional solutions, such as drywall. However, the differentiator among higher quality systems often comes down to durability, which both benefits the immediate project and establishes a longer-term timeline necessary to maximize profit potential.
To learn more about how STARC’s temporary wall systems can boost your project profitability, contact us today.