Healthcare Construction Leader Embraces Drywall Alternative for Cost Savings
W.E. Bowman, a healthcare construction leader based in Richmond, Virginia, serves major healthcare clients such as Southside Regional Medical, Riverside Health Systems, Central Health Systems, Virginia Commonwealth University Health System, Universal Health Systems, and University of Virginia Health Systems. Their commitment to excellence includes finding the most effective ICRA barriers to meet strict infection control standards while maximizing ROI.
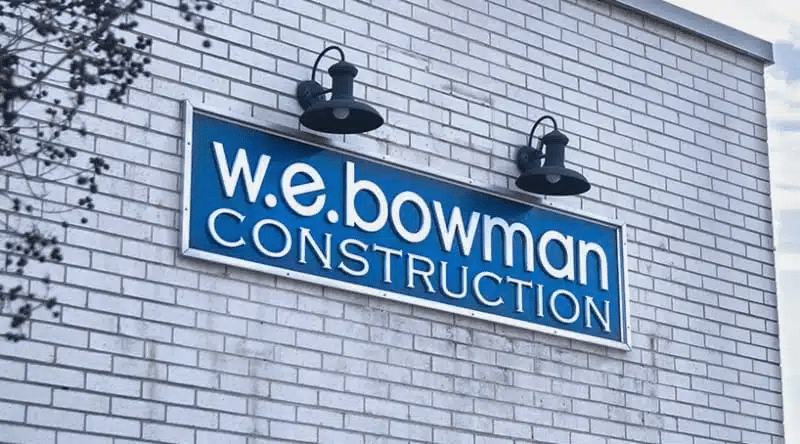
The Challenge
W.E. Bowman’s healthcare clients require that all temporary containment walls exceed ICRA Class IV/V requirements. The company also faced another challenge: identifying cost-effective, reusable ICRA barriers that could be used across multiple projects.
Traditionally, contractors turn to drywall for containment, but this approach has several drawbacks—it’s expensive over time, labor-intensive, and environmentally wasteful. Each renovation phase requires new drywall construction, which is ultimately discarded, driving up costs and creating unnecessary waste.
“With every new healthcare project, we would do the same thing—create temporary drywall barriers, only to throw them in the dumpster,” said Jerry Baker, W.E. Bowman’s Executive Director of Construction. “This provided no value to our company or our clients. We spent a lot of money on those walls, and they created their own problems. First, they took more time and money to construct. Second, we had to build a temporary plastic wall and create a negative air environment before we could even start building a metal stud wall.”
Another key concern for healthcare clients was aesthetics. “Depending on where the construction is taking place in the hospital, the customer wants the temporary wall to look like a permanent wall,” Jerry added.
The Solution: Reusable ICRA Barriers
A carpenter by trade, Jerry searched for a containment system that was reusable, offered a real-wall appearance, and met ICRA Class IV/V requirements.
“I saw STARC Systems featured at the ASHE national conference and in industry publications. Having worked in healthcare construction for many years, I was searching for an alternative to drywall that would give us a competitive edge,” Jerry said.
W.E. Bowman invested in STARC’s reusable modular ICRA barriers, which provided long-term cost savings and significantly reduced material waste. After just five project phases, the investment had paid for itself.
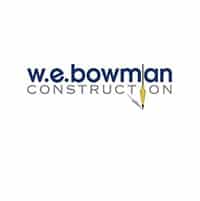
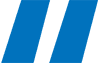
We considered our return on investment with STARC and it’s paid off. You really want a product that has proven endurance when you work in healthcare. We know our STARC panels will last us for a number of years and we can use STARC on hundreds of projects.
– Jerry Baker, Executive Director of Construction, W.E. Bowman
ROI: A Cost-Effective Alternative to Drywall
Here’s how STARC ICRA barriers delivered measurable ROI for W.E. Bowman:
- The project required 5,200 feet of temporary containment spread over seven phases.
- The cost of STARC Systems was fully recouped after just five phases.
- Overall savings compared to drywall: 75%.
- The company plans to reuse the STARC panels on hundreds of future projects.
“We considered our return on investment with STARC, and it’s paid off,” Jerry said. “You really want a product that has proven endurance when you work in healthcare. We know our STARC panels will last us for a number of years, and we can use them on hundreds of projects.”
The Payoff: Performance and Aesthetics
The benefits extend beyond cost savings. Healthcare clients appreciate the professional appearance of STARC’s ICRA barriers, as well as their performance in infection control.
“They like the real-wall appearance and the convenience of the door systems,” Jerry noted. “Our healthcare clients know it meets ICRA Class IV requirements, and it works well with the pressure monitoring system. It’s just clean, and they love it.”
By replacing drywall with STARC Systems’ modular, reusable ICRA barriers, W.E. Bowman has transformed its approach to temporary containment—reducing costs, improving efficiency, and delivering a higher-quality experience for healthcare clients.
See How Much You Can Save with STARC Systems